MLCC/LTCC Manufacturing Equipment
What is MLCC?
MLCC is an acronym for multi-layered ceramic capacitors.
These chip-type capacitors are designed to be small and large-capacity thanks to multi-layered (laminated) ceramic dielectrics and metal electrodes.
The compact, heat-resistant design makes MLCC ideal for high-frequency circuits, with frequent adoption in computers, communication devices, video devices, automobiles, and most other digital devices.
In recent years, electronics have become more prominent in automobiles, smartphones have continued to become more sophisticated, and IoT (Internet of Things) has become increasingly popular. This has brought a rapid increase in demand for MLCC, which have proven to be highly versatile electronic products.
What is LTCC?
LTCC is an acronym for low temperature co-fired ceramics. Because these ceramics are fired at low temperature, it is possible to use low-resistance metal as the conductor, reducing resistance loss. This makes them suitable for high-frequency applications. As wiring patterns can be formed on the surface layer and on the inner layers, lamination and flattening can be performed easily. In addition, due to the small variation in contraction, high-precision and high-density mounting are possible. These ceramics are expected to be used in a wide range of fields including circuit boards and semiconductor packages.
JTEKT Thermo Systems MLCC and LTCC Production Heat Treatment Equipment
As a manufacturer of heat treatment equipment for MLCC/LTCC production, JTEKT Thermo Systems strives to solve various customer problems by using advanced technology and high-reliability manufacturing supported by an extensive delivery history.
Although the company is able to provide a wide variety of equipment as a general manufacturer of heat treatment equipment, this page introduces some representative JTEKT Thermo Systems products.
Processing Applications
JTEKT Thermo Systems heat treatment equipment for MLCC/LTCC production is generally used for debinding and firing, reoxidation, and electrode firing, but the equipment can also be designed to meet various customer-specific requests, including intermediate processing applications.
Features and Strengths
Manufactured according to the varied individual experiences of the manufacturer, MLCCs and LTCCs do not have a designated “standard” when it comes to manufacturing.
In addition to its heat treatment equipment platform of simple, inert gas ovens and continuous mesh belt-type furnaces, JTEKT Thermo Systems regularly provides one-of-a-kind customer-specific equipment.
JTEKT Thermo Systems supports high-quality MLCC and LTCC manufacturing through advanced atmosphere control and heating control technology developed through years of experience.
Products
-
Mesh Belt Type Continuous Furnace
Heat treatment furnace with continuous mesh belt conveyance
Applications :
MLCC debinding (Binder burn out), and electrode baking, LTCC firing -
Ceramic Conveyor Type Continuous Furnace
These products use a ceramic chain with excellent heat and wear resistance in the transport conveyor.
Applications :
MLCC firing, reoxidation -
Inert Gas Oven
Hot air circulation oven for heat treatment in nitrogen (N2) atmospheres with a low oxygen (O2) concentration of 20 ppm or less
Applications : Debinding (Binder burn out)
-
Series
Manufacturing equipment with superheated steam atmospheres to meet a wide variety of needs
Applications :
Debinding (Binder burn out) -
Vacuum Purge Type Box Furnace
With rapid pump-down performance, gas change to a nitrogen (N2) atmosphere can be completed in a short time.
Applications :
MLCC secondary debinding
LTCC firing -
Exhaust Gas Treatment Equipment
Exhaust gas treatment equipment that uses an electric heater to enable a direct combustion method
Applications :
Combustion decomposition of exhaust gas
Mesh Belt Type Continuous Furnace
With a mesh belt construction and the adoption of a muffle, these furnaces offer excellent atmosphere stability and reproducibility. This makes them ideal for MLCC debinding, electrode firing, and LTCC firing.
Since delivering the first furnace for the Japanese electronics industry in 1980, JTEKT Thermo Systems has shipped over 4,000 mesh belt type continuous furnaces for manufacturing electronic components.
The adoption of a metal muffle delivers excellent temperature uniformity inside the furnace. In addition, the furnace atmosphere offers excellent airtightness as well as improved stability and reproducibility.
Adopting Moldatherm heaters featuring JTEKT Thermo Systems’ heat insulation technology and advanced temperature variation characteristics ensures high-precision temperature control as well as excellent energy savings. This makes these products ideal for heat treatment lines in MLCC and LTCC manufacturing.
An optional lineup of units for processing the organic exhaust gases generated during debinding is also available, ensuring a wide selection of processing equipment suitable for any application.
Multi-inlet/exhaust type
With a muffle structure featuring multiple inlets and exhausts according to the work being processed, these models allow for fine-tuned atmospheric adjustment.
Products can be designed according to customer requests, such as with MLCC copper electrode baking requiring highly efficient debinding, or processing requiring atmospheric changes at each step.
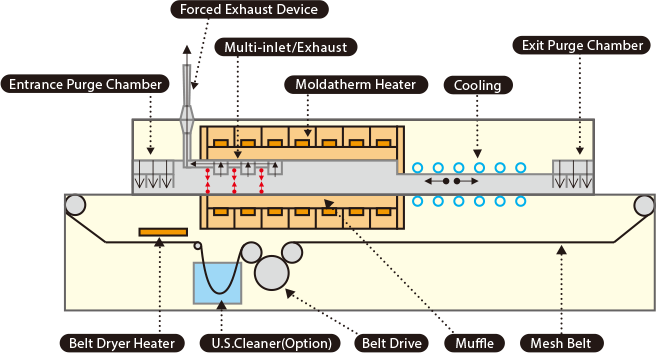
Processing application examples
Applications
Scroll →
Industrial field | Purpose of heat treatment | Heat-treated product |
---|---|---|
Electronic components |
・Drying ・Curing ・Debinding (Binder burn out) ・Electrode Baking ・Reoxidation ・Calcinating ・Firing ・Annealing ・Sintering ・Soldering ・Silver Brazing |
・Reactor ・MLCC (Multi-Layer Ceramic Capacitor) ・Multilayer Inductor ・LTCC (Low Temperature Co-fired Ceramics) ・Hermetic Terminal ・Ferrite Core ・Piezoelectric Element ・Ceramic Package ・Reoxidation |
Others |
・Drying ・Curing ・Debinding ・Annealing ・Electrode Baking ・Overcoating |
・Photovoltaic ・Bonded Magnet ・Sintered Magnet ・Metallic Material |
Specifications
Max. operating temperature | 1000℃ |
---|---|
Transport method | Mesh belt conveyance |
Heating chamber | Heat-resistant steel muffle |
Belt width (mm) | 150 to 800 |
Supported atmospheres | N2, N2 (wet), N2 + air, Air |
Options | Belt cleaner, detachable air inlet/exhaust unit, exhaust gas treatment unit, workpiece conveyor * Various other options are also available. Click here to contact JTEKT Thermo Systems. |
Organic exhaust gas treatment units
-
Heater type exhaust gas treatment unit
-
Catalytic exhaust gas treatment unit
-
Water-cooled cold trap
Ceramic Conveyor Type Continuous Furnace
These products use a ceramic chain with excellent heat and wear resistance in the transport conveyor. The designs are compact and deliver superior energy-saving performance. They are ideal for MLCC reoxidation processes.
Compared to other high-temperature furnaces such as roller transport and pusher transport, chain transport provides more stable transport with less transport trouble related to the firing jigs.
The lineup features alumina chains (max. 1200°C) and high-temperature specification mullite chains (max. 1400°C).
Specifications
Max. operating temperature | 1400°C (ceramic muffle) 600°C (heat-resistant steel muffle) |
---|---|
Transport system | Ceramic conveyor transport |
Heating chamber | Heat-resistant steel muffle or ceramic muffle |
Supported effective widths | Minimum 200 mm (For other widths, please contact us.) |
Supported atmospheres | Air, N2 (wet/dry) |
Applications | MLCC firing and reoxidation, glass glazing, ferrite sintering, thermistor firing, ceramic sensor firing |
Inert Gas Oven
These high-performance inert gas ovens are capable of heat treatment at temperatures of up to 600°C in atmospheres with oxygen concentrations as low as 20 ppm. This makes them ideal for MLCC and LTCC debinding.
JTEKT Thermo Systems developed its inert gas ovens and clean ovens following development of basic technologies cultivated from atmospheric oven production. The company has now delivered over 4,000 ovens.
Featuring a proprietary chamber structure and sealing technology, these inert gas ovens provide excellent air-tightness and temperature uniformity while also ensuring improved stability and reproducibility.
In addition, the adoption of an external cooling mechanism powered by a cooling blower makes it possible to perform rapid cooling without affecting the furnace atmosphere, allowing for shortened processing times.
An optional lineup is also available—including organic exhaust gas treatment units and increased-safety specifications required for equipment dedicated to debinding—to ensure safe and secure MLCC and LTCC production.
Applications
Scroll →
Industrial field | Purpose of heat treatment | Heat-treated product |
---|---|---|
Electronic components |
・Debinding (Binder burn out) ・Annealing ・Curing |
・Ceramic materials/sheets ・MLCC (Multi-Layer Ceramic Capacitor) ・LTCC (Low Temperature Co-fired Ceramics) ・Ceramic O2 sensor ・Ferrite Core ・FPC (Flexible printed circuits) ・Common-mode noise filter ・Thermistor |
Others |
・Debinding ・Curing ・Annealing ・Firing ・Drying |
・Silicon carbide ceramics ・Electrostatic chucks ・Aluminum nitride ・Optical lens ・Flexible substrate ・Rechargeable battery electrode material ・Wire Harness(Copper wire) ・catalyst ・Forged products |
Specifications
Method | Forced air circulation (side flow) |
---|---|
Max. operating temperature | 600℃ |
Regular operating temperature range | RT + 60 to 600°C |
Supported atmospheres | N2, Air |
Internal dimensions (mm) | 600W × 600H × 600D (INH-21CD) to 1000W × 1000H × 1000D (INH-100CD) |
Cooling mechanism | Forced cooling mechanism with exterior tank |
Options | Oxygen analyzer, exhaust gas treatment unit, increased-safety specifications, workpiece loading lifter * Various other options are also available. Click here to contact JTEKT Thermo Systems. |
Custom examples
-
Custom model with lifter
-
Optional debinding specification
-
Heater type exhaust gas treatment equipment
A note on safety
In situations where binders and organic components are generated during product processing, ensure safety by performing treatment that considers the heating rate, amount of gas introduced, and other factors based on the differential thermogravimetric curve and other characteristics of the generated component.
Exhaust Gas Treatment Equipment
This equipment uses a high-temperature direct combustion method to accurately purify the organic vapor generated from the product being treated. This makes them ideal for the exhaust gas treatment of heat treatment equipment that performs debinding.
Vapor containing organic compounds is generated from the object being treated during the temporary sintering process of ceramics and the degreasing process of electronic components. This gas, which diffuses in the furnace atmosphere, is discharged from the heat treatment equipment as exhaust gas. However, this gas has a powerfully irritating odor and is combustible, so it may lead to a poor work environment and pose fire and explosion hazards. The countermeasure against these issues is to purify the gas, but how to do so is the challenge.
JTEKT Thermo Systems has released the exhaust gas treatment equipment, which uses a direct combustion method to accurately purify the exhaust gas, thereby improving both the work environment and its safety. Currently, over 700 units are in operation on production lines around the world.
The direct combustion method has a structure that is simpler than that of the catalytic combustion method and has high tolerability for tar and dust, which enables its use in the exhaust gas treatment of a wide range of objects being treated.
This equipment adds fresh air to the exhaust gas and accurately performs direct combustion decomposition of the organic matter within the muffle heated to a temperate at or above the ignition point (up to 850°C). An electric resistance heater (a Moldatherm heater made by JTEKT Thermo Systems) is used for the heat source, so there is no need to install fuel gas and other such utilities that were required for the gas burner method, which burns the target with an open flame. This reduces the cost at the time of equipment installation. Highly reliable Moldatherm heaters enable stable exhaust gas treatment with their excellent energy saving performance and temperature control.
We recommend that this equipment be used as a set with an inert gas oven, a degreasing furnace, or a mesh belt type continuous furnace. Combining this equipment with JTEKT Thermo Systems heat treatment equipment enables linked operation and interlocking, which ensures more efficient and safer operation.
-
Internal structure
-
Usage example (linked with an inert gas oven)
Specifications
Exhaust gas treatment method | Direct combustion by way of heating provided with an electric heater |
---|---|
Max. operating temperature | 850°C |
Heating chamber | Heat-resistant steel muffle |
Air to aid combustion | Compressed dry air |
Treated gas amount | 400 L/min (GM-30N1) to 800 L/min (GM-50N1) * Including the air to aid combustion |
Series
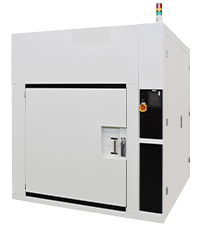
To provide heat treatment technology that meets the needs of all customers, JTEKT Thermo System has developed a manufacturing equipment series that utilizes a superheated steam atmosphere.
These heat treatment devices are available as batch or continuous types. JTEKT Thermo System also offers a lineup of products for experimental development R&D, small-volume production, and mass production.
Superheated steam
Superheated steam is colorless, transparent, high-temperature steam gas (H2O) generated by heating saturated steam evaporated at 100°C to an even higher temperature under normal pressure.
Main features
- Higher specific heat than heated air and better radiation effects for uniform heating in less time
- Low-oxygen processing capabilities
- Improved productivity and reduced running costs through accelerated hydrolytic reactions of processed products
Processing applications
- De-binding and baking of electronic components
- Debinding (Binder burn out) of ceramic parts
- Drying and degreasing of metal parts
- Removal of resin
- Heat treatment of products for which heating efficiency cannot be improved through conventional methods
* The effectiveness varies depending on the material being treated. We recommend testing with our demo unit first to verify effectiveness.
Example application results
- Half the required heat-up time in de-binding of electronic components
- Lower processing temperatures
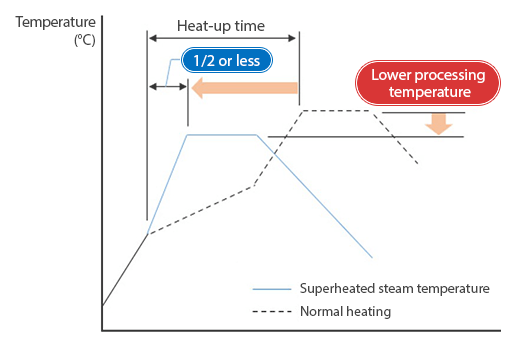
Batch-Type
AllFit Inert Gas Oven with Superheated Steam
Specifications
Model | AF-INH21 | AF-INH100 |
---|---|---|
Max. temperature | 600℃ | |
Normal temperature | RT + 60 to 600°C | |
External dimensions (mm) | 1485 (W) × 1700 (H) × 2090 (D) | 1850 (W) × 2425 (H) × 2593 (D) |
Test area dimensions (mm) | 600 (W) × 600 (H) × 600 (D) | 1000 (W) × 1000 (H) × 1000 (D) |
Treatment atmosphere | Superheated steam, N2, Air | |
Residual oxygen concentration | 20 ppm or less (when superheated steam is introduced; reference value) Note: May vary depending on the amount of dissolved oxygen in the supplied water. |
* Additional safety features included (relief door and reinforced door)
Batch-Type High-Temperature
AllFit Atmospheric Box Furnace with Superheated Steam
Specifications
Model | AF-µBF |
---|---|
Max. temperature (*1) | 1000℃ |
Normal temperature (*1) | 400 to 900°C |
Effective internal muffle dimensions | 200 (W) × 200 (H) × 400 (D) |
Treatment atmosphere | Superheated steam, N2, Air, H2 |
Residual oxygen concentration | 20 ppm or less (when superheated steam is introduced; reference value) Note: May vary depending on the amount of dissolved oxygen in the supplied water. |
*1 Values are for temperatures measured inside the heating chamber and outside the muffle.
Continuous-Type
AllFit Compact Conveyor Furnace with Superheated Steam
Specifications
Model | AF-810A |
---|---|
Max. temperature | 1000℃ |
Normal temperature | 250 to 900°C |
Treatment atmosphere | Superheated steam, N2, Air |
Belt width (mm) | 200 |
In-furnace passing height (mm) | 30 |
Zone configuration | Inlet/outlet purge chamber, 7 heating zones (1704 mm), cooling chamber (450 mm) |
Residual oxygen concentration | 20 ppm or less (when superheated steam is introduced; reference value) Note: May vary depending on the amount of dissolved oxygen in the supplied water. |
Vacuum Purge Type Box Furnace
With rapid pump-down performance, gas change to a nitrogen (N2) atmosphere can be completed in a short time.
With large internal capacity and high efficiency, this furnace is ideal for production. This is a multipurpose heat treatment furnace that is suitable for production of LTCC substrates and MLCC.
JTEKT Thermo Systems offers an extensive lineup of atmospheric furnaces for experiments that are capable of heat treatment from 400°C up to a maximum temperature of 1800°C. Based on the technologies that we have developed through the manufacture of these furnaces and our vacuum and atmosphere control technologies, we have further refined our large-volume box furnaces capable of heat treatment in a wide range of atmospheres. These furnaces can be used for mass production.
The heater and thermal insulation utilize our original Moldatherm heater, with excellent thermal insulation performance and maintainability, for a system that delivers high-precision temperature control and superior energy savings.
By performing vacuum purge, it is possible to shorten the time required to change the atmosphere inside the furnace.
An optional lineup of units for processing the organic exhaust gases generated during debinding is also available, and can be used for MLCC debinding and LTCC firing.
Specifications
Model | MB |
---|---|
Max. operating temperature | 1000°C |
Ordinary operating temperature range | 400 to 900°C |
Internal capacity | Max. 400 L |
Withstand load | Max. 200 kg |
Applications | MLCC secondary debinding, LTCC firing |
Demonstration and test areas
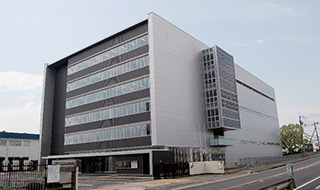
Comprehensive manufacturer of heat treatment equipment, which solves heat treatment problems from different fields beyond the boundaries of fields and areas
From equipment for research and development to production facilities, by assembling technicians in major business areas for vitalization of new products and technology development, and by installing our demonstration equipment for experiments and evaluations, JTEKT Thermo Systems is not only developing processes of its own but also providing the system that can be used for customers’ pre-tests and for performance evaluation.
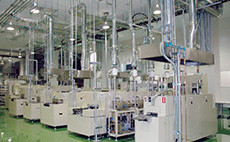
Continuous furnace area for electronic component manufacturing
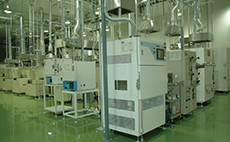
Compact electric furnace & oven area
About JTEKT Thermo Systems
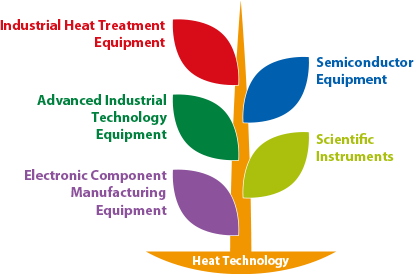
The metallic components, ceramics, etc. of formed and fabricated materials that form the foundation of the industry; the semiconductors and electronic components that support the latest technologies; the displays that enrich people's lives and next-generation batteries that control global environment pollution; and experimental developments to create all of these industries—it is not an overstatement to say that the heat treatment equipment created by JTEKT Thermo Systems is involved in all of the industries in our lives. With the unique technology created by the "Technology Tree" that fused the five pieces of "Technology Leaves" that were cultivated with a history spanning half a century, we continue to contribute to every field in the world.
International Offices
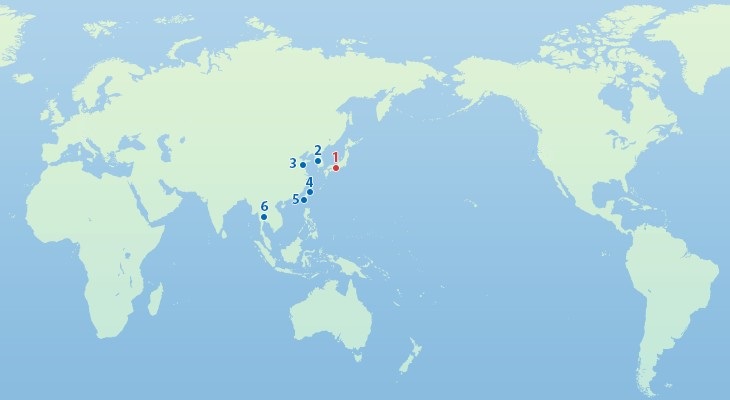
HEAD OFFICE
1. JAPAN (Tenri)
JTEKT Thermo Systems Corporation
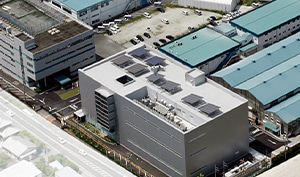
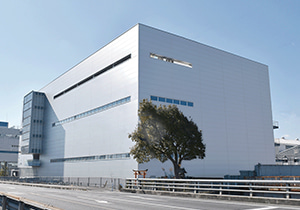
-
JTEKT THERMO SYSTEMS KOREA CO., LTD.
-
3. CHINA (Shanghai)
JTEKT THERMO SYSTEMS (SHANGHAI) CO., LTD.
-
4. TAIWAN (Taipei)
JTEKT THERMO SYSTEMS TAIWAN CO., LTD.
-
5. TAIWAN (Taichung)
JTEKT THERMO SYSTEMS TAIWAN
TECHNICAL SERVICE OFFICE IN TAICHUNG -
6. THAILAND (Bangkok)
JTEKT MACHINERY (THAILAND) CO., LTD.